Vše o svařování laserem | MEPAC článek
Úvod do problematiky
Na čem je založena technologie svařování laserem u vstřikovacích forem?
| Kam zaostřím, tam navařím
Velkou výhodou laserového svařování či navařování u vstřikovacích forem je skutečnost, že laserový paprsek získává hustotu energie potřebnou k vytvoření svárového bodu až po zaostření paprsku, ke kterému dochází v tzv. ohniskové vzdálenosti, která bývá v praxi okolo 150 mm (vzdálenost zaostřovací čočky od zaostřeného bodu). To uživateli poskytuje dobrý prostor pro manipulaci s laserovým paprskem tak, aby se dostal i do komplikovaných nebo hlubokých tvarů, kam se jinými metodami není možné dostat.
| Více tepla, více škod
Teplo, které je potřebné pro roztavení svařovaného obrobku nebo navařovaného materiálu, je získáváno z přenosu energie při dopadu již zmíněného zaostřeného laserového paprsku na tavený materiál. Laserový paprsek přitom může nést energii spojitě, kdy se jedná o CW laserové zdroje anebo ve formě pulsů, kde hovoříme o QCW laserových zdrojích.
Pro technologii laserového svařování a navařování je vhodnější využití QCW technologie z důvodu menšího množství tepla vnášeného do navařovaného materiálu, protože poskytujeme časový prostor na odvod tepla z navařovaného místa. Optimální množství tepelné energie vytvořené na místě dopadu laserového paprsku je důležité. Nadměrné množství vneseného tepla může vést ke změnám původní tvrdosti materiálu či dokonce ke změně celkového tvaru.
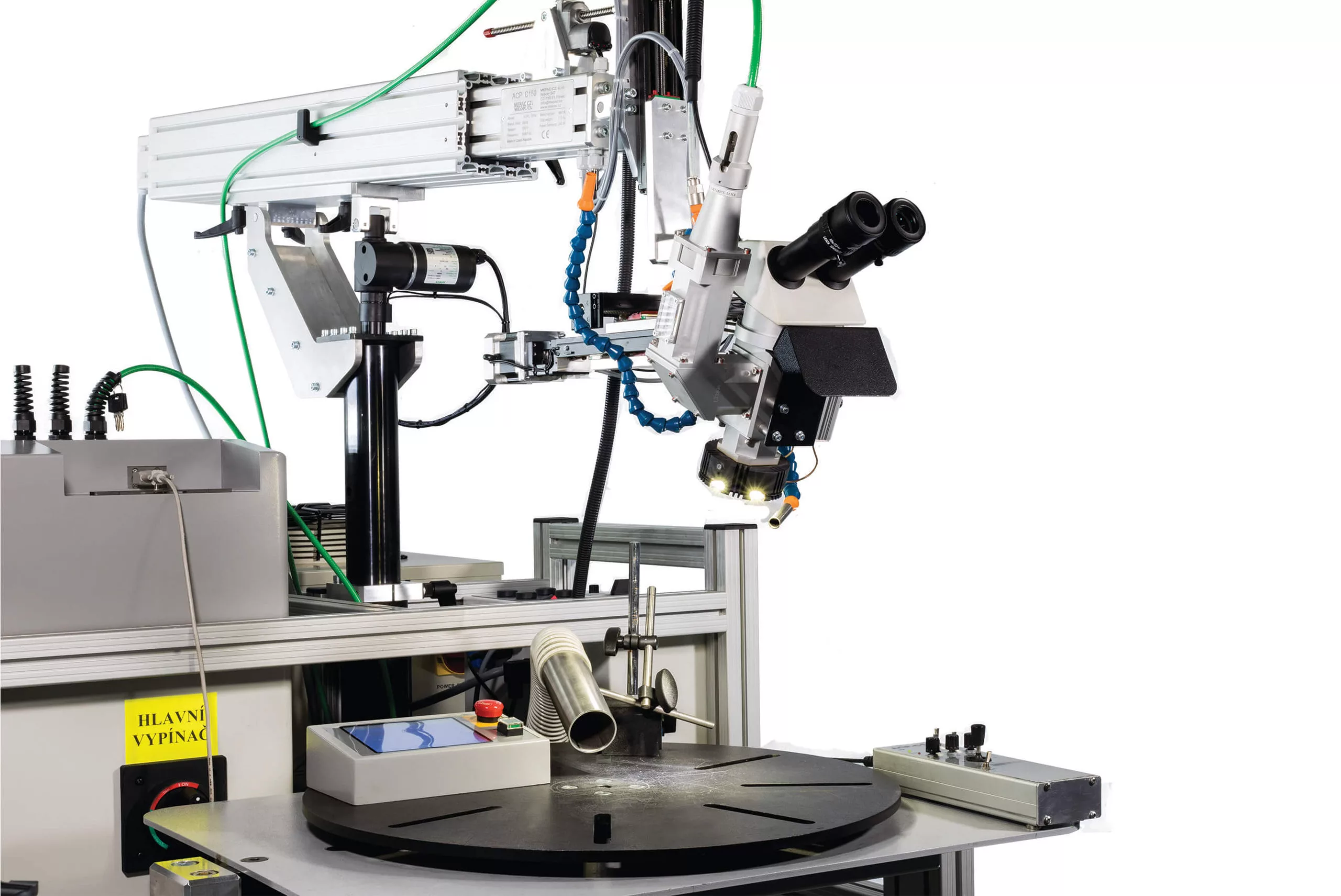
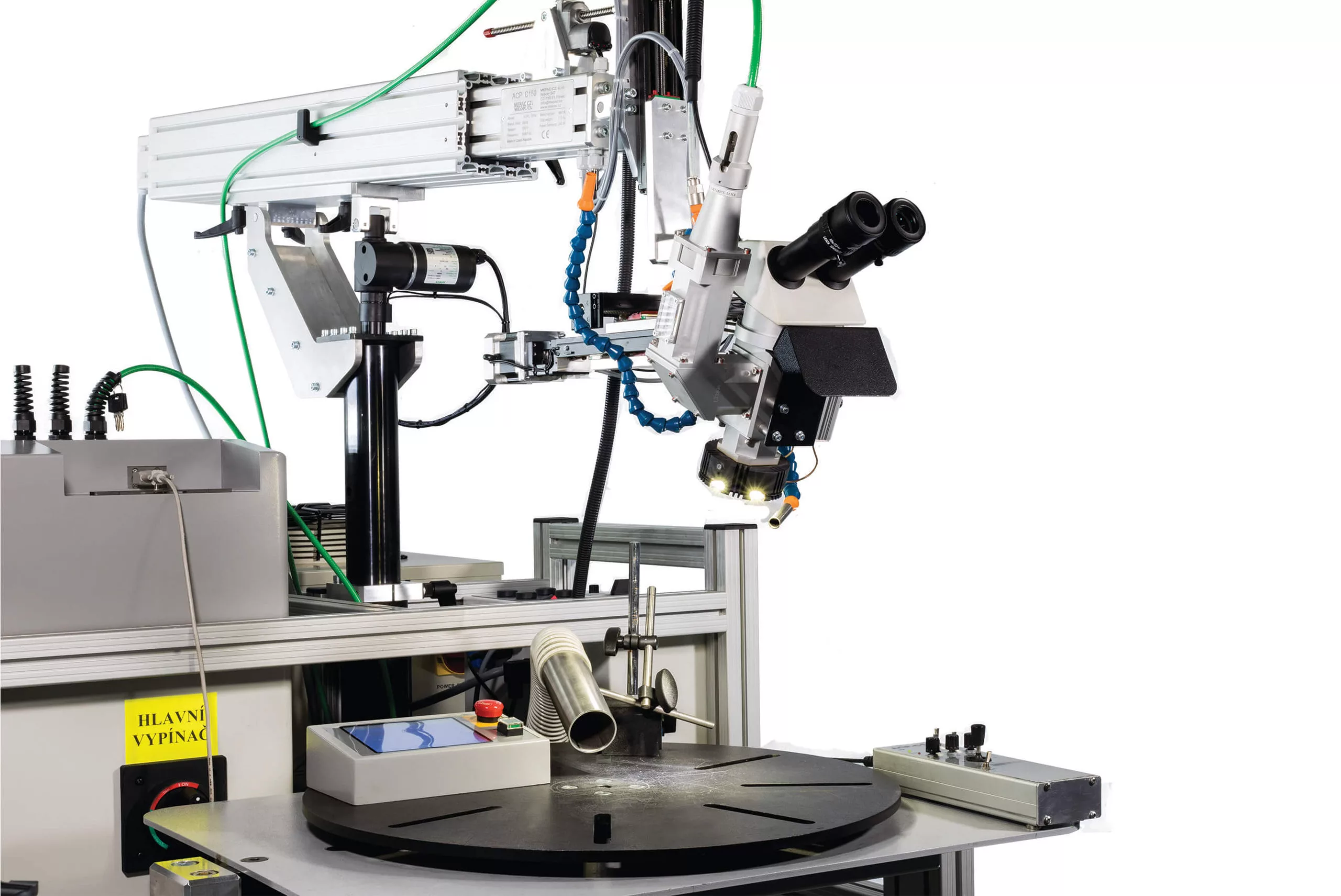
| Optimální vlnová délka
Vstřikovací formy či jejich části jsou vyráběny zejména z nástrojových ocelí (kalených i nekalených), slitin hliníku (prototypové formy) a slitin mědi (jádra pro optimalizaci tepelného procesu). U všech výše uvedených materiálů musí být zaručena dobrá, pokud možno maximální přeměna energie laserového paprsku na tepelnou energii v místě dopadu. Z tohoto pohledu je optimální volbou vlnová délka laseru okolo 1070 nm, což splňují Nd:YAG laserové zdroje a vláknové laserové zdroje.
U některých aplikací jsme se sice setkali i s použitím speciálních materiálů, jako je např. PtRh10 či jiných vzácných kovů, jako jsou zlato a stříbro, ale tyto tvoří jen menší část.
Výhody oproti standardním postupům
| Nejpřesnější a nejšetrnější metoda
Mezi běžně používané standardní svařovací postupy patří systémy pracující s netavící se wolframovou elektrodou typu TIG (WIG) či plasmové systémy a systémy pracující s tavnou elektrodou tvořenou přídavným drátem typu MIG/MAG systémy.
Pro navařování forem lze využít TIG a plasmu, MIG/MAG je z výše zmíněných metod nejméně přesná a do svařovaného obrobku vnáší nejvíce tepla. Plasmové systémy umožňují dosažení menšího svarového bodu oproti TIG systémům. Plasmové i TIG systémy pak mohou pracovat se spojitou nebo pulsní energií, která umožňuje další minimalizaci vnášeného tepla. Nicméně obě metody vnášejí výrazně více tepla než svařování za pomoci laseru, jenž je schopný vytvořit potřebnou energii na velmi malém prostoru.
Další nevýhodou standardní svařovací technologie může být polohování wolframové elektrody ve složitých tvarech. Špičku elektrody je nutné držet ve vzdálenost 3-5 mm od svařovaného povrchu, což při svařování komplikovaných tvarů přináší řadu problému, jako je například: přeskok oblouku na jinou stěnu výrobku, ulpívaní wolframové elektrody na stěnách svařence atd. Následné odstranění vzniklých vad s použitím této technologie je časově náročné.
| Shrnutí výhod svařování laserem:
- Malé vnášené teplo do obrobku
- Malá tepelně ovlivněná oblast obrobku
- Větší odstup laserové hlavy od povrchu, což umožňuje svařování výrazně složitějších tvarů
- Maximální dosažitelná tvrdost (samokalitelného) návaru může být až 60 HRc
- Laserové svařování a navařování patří mezi nejpreciznější a nejpřesnější metody svařování
- Pro systémy s vlastní konstrukcí:
– Motorizované pojezdy laserové hlavy umožňují vytváření kvalitních návarů, velmi tenkých hran, navařovaných ploch a 3D tvarů, a to i ve větších rozměrech - Pro systémy s kolaborativním robotem:
– Proces navařování lze řídit manuálně, ale také jej lze i programovat
Rozdíl mezi svařováním a navařováním laserem
| Svařování
Při svařování dopadá laserový paprsek na dvě části obrobku, které se v místě dopadu zahřejí tak, že mezi nimi dochází k vytvoření taveniny, jejímž následným vychladnutím dojde k vytvoření pevného spojení mezi těmito částmi, tedy sváru. Tato skutečnost v praxi většinou vede k tomu, že v místě sváru je patrný propad vůči okolnímu povrchu a také k tomu, že zejména u kalených ocelí jsou sváry a jejich okolí náchylné na tvorbu prasklin.
Poznámka:
Podobné vlastnosti, jako má pro svařování laserový paprsek, má i elektronový paprsek. Systémy s elektronovým paprskem se používají pro svařování vysoce reaktivních kovů, jako je titan (např. v letectví). Kvůli reaktivnosti těchto kovů dochází k jejich svařování ve vakuu, proto nejsou tyto systémy vhodné pro navařování forem.
| Navařování
Při navařování roztavuje laserový paprsek přídavný materiál (ten může být ve formě návarového drátu nebo prášku) a následně i navařované místo. Návarový materiál je možné přidávat automaticky pomocí podavače. Složité tvary forem se však doposud navařují výhradně s manuálním podáváním drátu.
Pro navařování forem existuje cca 30 typů návarových drátů, ty jsou běžně k dispozici v průměrech od 0,2 do 0,8 mm. Vhodnou kombinací návarového materiálu s původním materiálem formy je možné dosáhnout původních tvarů se stejnými, ale dokonce i lepšími vlastnostmi, než měl původní materiál. A to jak z hlediska chemického složení, tvrdosti či houževnatosti navařené oblasti, což má vliv i na následné renovace poškozených zrcadlově vyleštěných či chemicky dezénovaných ploch.
Typy laserových svářeček
Laserové svářečky lze dělit dle různých hledisek. Může se jednat například o rozdělení z hlediska bezpečnostní třídy, dále dle použitých laserových zdrojů, z hlediska přivedení laserového paprsku anebo také dle jejich vybavení. Tzn. zda jdou vybaveny pracovním stolem, odsáváním anebo zda mají jednu či dvě ofukovací hubice pro přívod argonu. U většiny laserových svářeček jsou tyto parametry volitelné či přizpůsobitelné v závislosti na požadavcích zákazníka.
| Bezpečnostní třída
Protože má laserový paprsek u laserových svařovacích systémů značný výkon, je nutno zajistit ochranu operátora a pracovníků v okolí tak, aby nemohlo dojít k poškození jejich zdraví, zejména zraku přímo dopadajícím či jakkoliv odraženým laserovým paprskem. Laserové svářečky tak můžeme dělit na systémy v bezpečnostní třídě 1 a bezpečnostní třídě 4.
Bezpečnostní třída 1
Laserové systémy bezpečnostní třídy 1 jsou systémy, které mají pracovní prostor omezený pracovní kabinou, ze které laserový paprsek nemůže uniknout do okolního prostředí. Do prostoru pracovní kabiny je umístěný díl, s kterým lze pohybovat ručně nebo motoricky. Výhodou těchto kabin je možnost použití v různých prostorách. Nevýhodou těchto kabin je omezený pracovní prostor a nosnost pracovního stolu, proto se tyto systémy pro navařování vstřikovacích forem výrazně neprosadily.
Bezpečnostní třída 4
Laserové systémy v bezpečnostní třídě 4 jsou systémy, jejichž laserový paprsek vystupující z laserové hlavy není od okolního pracovního prostředí odstíněn a díky tomu je možné navařovat formy i o maximálních rozměrech a hmotnostech. Použití těchto laserových systémů je možné pouze ve dvou případech:
-
- Laserový systém je umístěn v samostatném pracovním prostoru odděleném od ostatních pracovišť tak, aby nemohlo dojít k úniku laserového paprsku ven z pracoviště, a tím ohrozit ostatní pracovníky. V praxi se to nejčastěji řeší samostatnou místností, na kterou jsou dle příslušného předpisu kladeny další speciální požadavky.
- Pro případy, kdy uživatel potřebuje pracovat s laserem přímo ve výrobní hale, je nutno kolem laseru vystavět speciální buňku ze speciálních certifikovaných materiálů, zabraňující úniku laserového paprsku mimo tuto buňku.
Pracovníci v těchto prostorách musí používat speciální ochranné oděvy včetně speciálních brýlí pro ochranu zraku, které musí být v souladu s parametry laseru.
| Ruční svařovací laser
U laserových svářeček využívajících metodu CW se v poslední době rozmáhá tzv. ruční svařovací laser. Jedná se o vláknový laserový zdroj s ovládáním, spojený s laserovou hlavou kabelem, obsahujícím optický kabel, hadici pro přívod ochranného plynu (argon) a s eventuálním přívodem svárového drátu. Operátor drží laserovou hlavici v ruce a pojíždí s ní po svařovaném povrchu. Laserová hlavice rozmítá laserový paprsek po povrchu v nastavených obrazcích (např. typu O, X), čímž dochází k nastavení velikosti roztavení svařované oblasti a eventuálně i svárového drátu – svářečka může pracovat s drátem i bez drátu. Tyto systémy jsou vhodné zejména pro svařování produktů z plechů, kde jsou pak sváry vůči metodě MIG/MAG ve výrazně větší kvalitě a pro standardní aplikace mnohdy nevyžadují další opracování. Pro navařování forem však nejsou tyto svářečky příliš vhodné.
| Zdroj
Již jsme si řekli, že laserové svářečky můžeme rozlišovat podle použitých laserových zdrojů typu CW či QCW a také dle typu zdroje Nd:YAG či vláknový zdroj.
| Přivedené laserového paprsku
Další způsob, jak členit laserové svářečky, souvisí se způsobem přivedení laserového paprsku do laserové hlavy, což má vliv na polohování laserového paprsku na povrch vstřikovací formy. Podle toho je také můžeme dělit na systémy, které mají rezonátory připojené přímo k laserové hlavě a na systémy, které pro přenos laserového paprsku z rezonátoru využívají optický kabel.
Systémy s optickým kabelem umožňují výrazně větší rozsah manipulování s laserovou hlavou, a proto je možné přivést laserový paprsek i do takových tvarů, kde mají systémy s rezonátorem v laserové hlavě problém a musí nastavovat polohu formy pomocí jeřábu. To může být nejen časově náročnější, ale také méně bezpečné.
Systémy s optickým kabelem lze dále dělit na systémy s vlastní konstrukcí (např. ACP) a na systémy postavené na kolaborativních robotech (např. ROWES) – ty patří mezi nejmodernější typy. Oba tyto typy systémů lze také dále upravovat v závislosti na požadavcích zákazníka a umožnit tak jejich maximální využití v rámci konkrétní aplikace.
Jaké materiály lze svařovat laserem?
| Materiál vyžaduje dávku citu a znalostí
Nejvhodnějším materiálem pro svařování či navařování jsou slitiny železa a nejrůznější typy ocelí, svařovat lze i slitiny hliníku a mědi, vzácné kovy (např. Au, Ag, Pt), eventuálně i reaktivní kovy (např. titan).
U slitin hliníku a zejména mědi je nutno počítat s odrazivostí laserového paprsku od svařovaného povrchu, což vyžaduje použití odlišného nastavení laseru než u oceli apod. Nesprávné nastavení může vést až k poškození laserové hlavy. Titan vyžaduje velmi specifické nastavení; nesprávné nastavení vede k tvorbě nekvalitních svárů. Na odrazivost laserového paprsku od povrchu má také vliv kvalita povrchu – čím menší drsnost povrchu, tím více se paprsek odráží.
| Materiál a nastavení s rozvahou
Při navařování je vhodné jako návarový materiál volit materiál s co nejpodobnějším chemickým složením a co nejpodobnějšími mechanickými vlastnostmi (zejména tvrdost). Laserové návarové materiály jsou tzv. samokalitelné – jejich zchladnutím v ochranném plynu dochází k vytvoření jejich tvrdosti. Tuto tvrdost je následně možné měnit i dalším tepelným zpracováním, což se však v praxi používá zřídka. Při náročných navařovacích procesech je vhodné pracovat i s různými průměry téhož návarového materiálu – lze tak dosáhnout rozdílné vlastnosti návaru.
Pro optimální nastavení parametrů laserové svářečky, volbu strategie laserového navařování, volbu laserového návarového materiálu a práci s ním doporučujeme absolvovat odpovídající školení laserového navařování. To je u nás dostupné buď samostatně anebo společně s dodávkou zařízení (v případě vyžádání od zákazníka).
Výroba a vývoj svařovacích laserů MEPAC
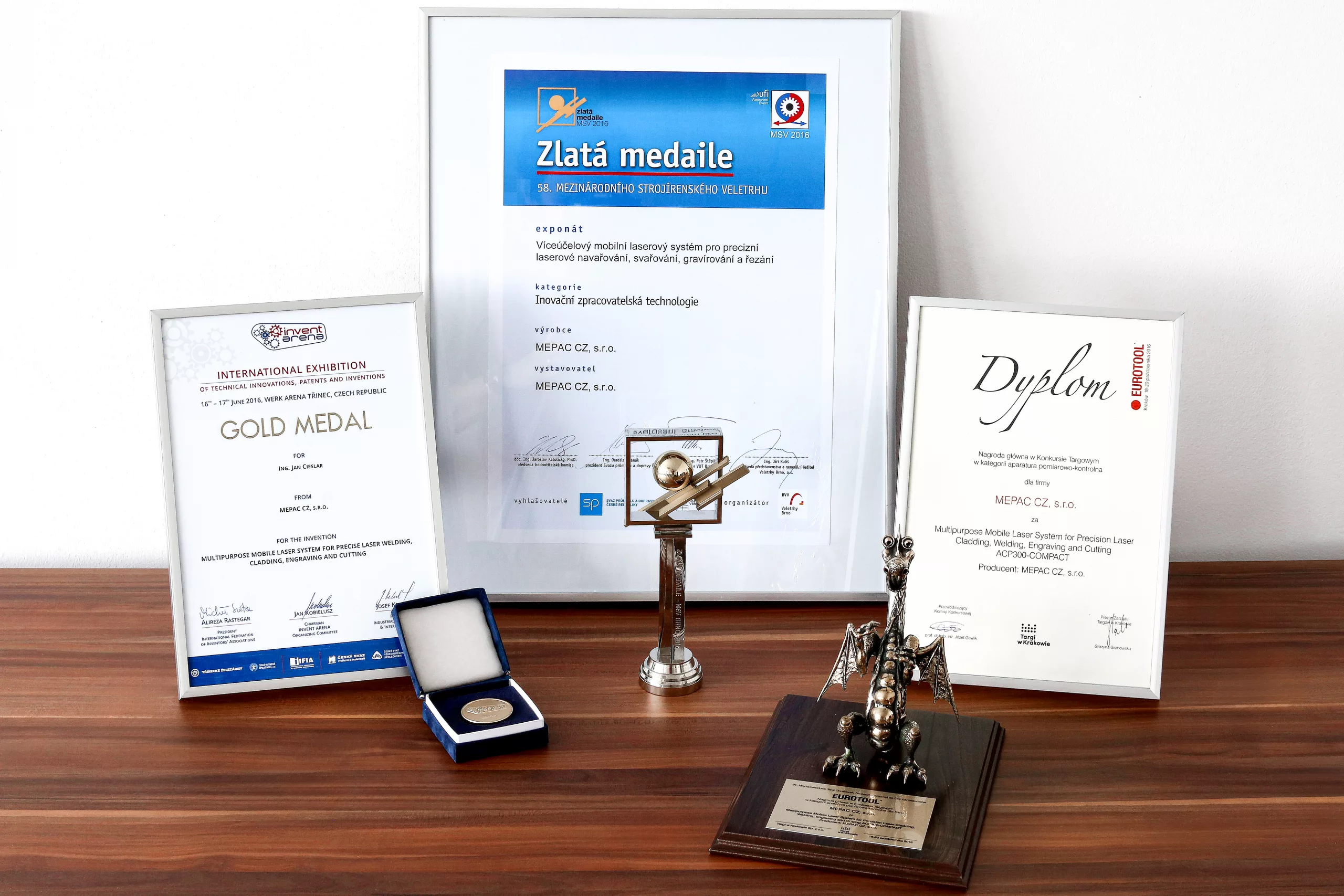
| 20 let zkušeností v oboru
Firma MEPAC se zabývá problematikou laserového svařování a navařování od roku 2003. Laserové svářečky vyvinuté a vyrobené ve firmě MEPAC obdržely na mezinárodních veletrzích v České republice, Slovensku a Polsku od roku 2004 šest zlatých medailí a jsou prodávány zejména v Evropě. Dlouhodobé zkušenosti nasbírané za tuto dobu, vlastní servis laserových svářeček, odborné poradenství a školení, dodávky laserových návarových drátů, laserových ochranných brýlí a dalšího příslušenství poskytují zákazníkům jistotu, že si nepořizují pouze svářečku, ale získávají také know-how potřebné k nejnáročnějšímu navařování nástrojů a forem v praxi.
Firma MEPAC je certifikována dle ISO 9001 od roku 2008, což zajišťuje dlouhodobou stabilitu výrobních procesů a kvalitu vyráběných laserových svářeček.
Školení a certifikace pro používání laserových svářeček
| Naučíme Vás vše potřebné
Našim zákazníkům nabízíme možnost absolvovat školení laserového navařování. Toto školení bývá v rozsahu 3 až 5 dní, kde se absolventi naučí pracovat s laserem tak, aby zvládli potřebné činnosti spojené s kvalitním laserovým navařováním forem. Naučí se strategii spojenou s navařováním a řešení některých problémových návarů. Vše si přitom mohou ověřit v praxi i na vlastních tvarových vložkách, které se na školení přinesou a se kterými se ve své praxi budou setkávat nejčastěji.
Absolventi školení obdrží certifikát a mohou obdržet také průkaz podepsaný registrovaným svářečským komisařem.
Ze světa laserových technologií
Ruční svařovací laser
RUČNÍ SVAŘOVACÍ LASERJinou svařovací metodou bychom to nezvládli..Přišel k nám zákazník se zajímavou výzvou, zavařit krytování o objemu 2m³ tudíž se jednalo o dlouhé sváry, které bylo třeba zavařit rychle a hlavně bez tepelného zatížení, aby nevznikla deformace...
Strojaři se seznámili s inovativní technologií Lase ONE
Budoucí posila pro přesné strojírenství? Dne 28.11.2022 jsme navštívili Střední průmyslovou školu a Obchodní akademii v Bruntále , abychom třídě 3.C předvedli inovativní technologii Lase ONE – mikrosvařování, která se využívá v přeném strojírenství....
Svět plastů | Jednoduché precizní mikronavařování forem
Fyzický stav vstřikovací formy, nástroje který slouží k sériové výrobě, má významný vliv na kvalitu a ekonomiku produkce plastových dílů. Havárie, opotřebeni, závady vzniklé v důsledku nevhodné manipulace a další poškození formy je potřeba urychleně řešit. Paleta...